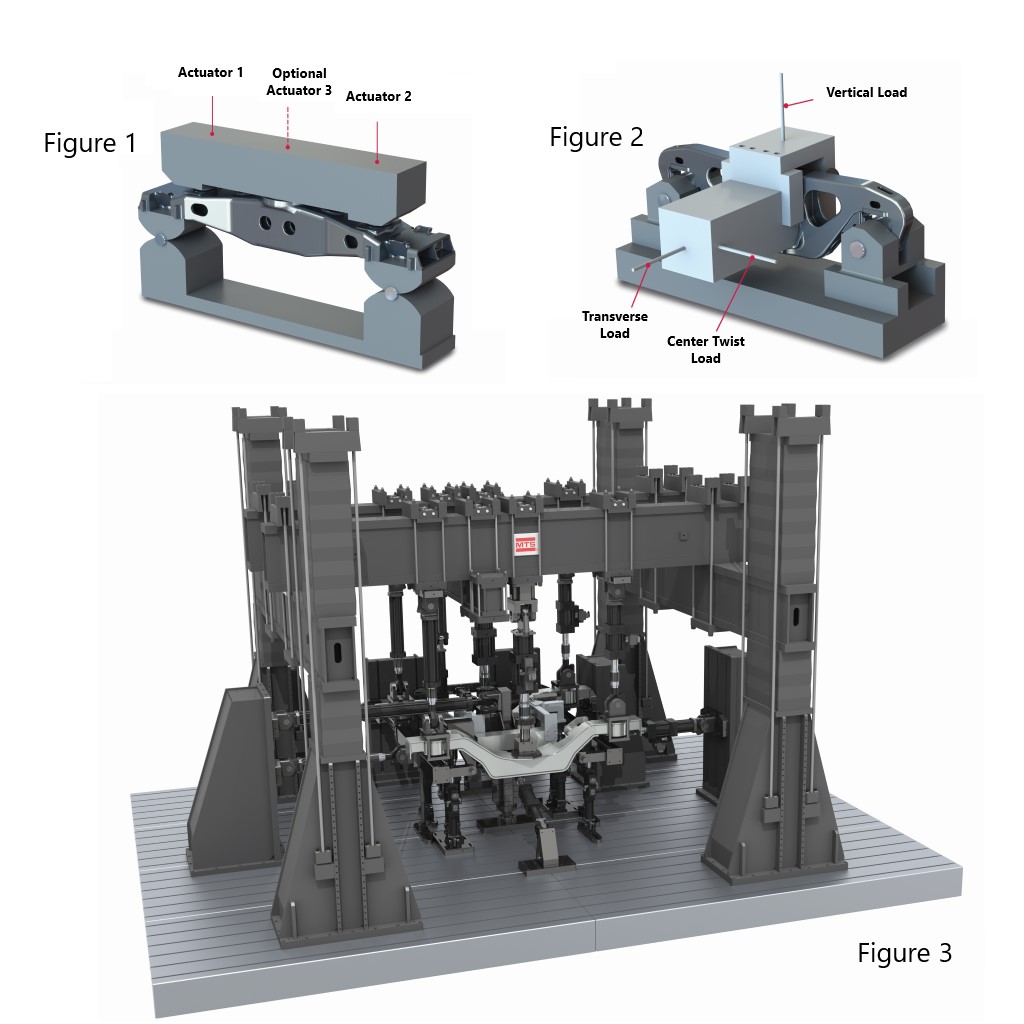
当考量构成铁道机车车辆系统的所有部件和子总成及其周围环境时,沿轨道顶部画一条虚线会有所帮助。这条线将该系统分为两个主要组。第一组为“铁道机车车辆”,位于线上方,主要含转向架构架(或两个侧框架和支撑架的组合)以及初级悬架、次级悬架和铁道机车车辆等。第二组为“道路”,位于线下方,主要含轨道、紧固件,轨枕、道砟及其他部件等。两组之间的连接点为带有一套转轮的车轴。
虽然这一系统中的许多较简单的因素可以通过基本的部件测试来处理,但评价铁道机车车辆中的部件或子总成需要考虑一下三项同样重要的因素:疲劳、性能和舒适度。
虽然疲劳寿命可能并非乘客在乘坐过程中所欣赏的(甚至考虑的),但这一因素仍然是铁道机车车辆设计和服务中非常重要的一部分。铁路行业自上个世纪起就已经了解并认识到疲劳测试在铁路部件设计和制造中的重要性。为确保持续的疲劳寿命和乘客安全,业界制定了多项认证标准。
符合认证标准
铁路部件和子系统制造商必须对部件和子系统进行测试,以符合相应的认证标准,相关认证标准包括适用于支撑架的 M-202-97、适用于侧框架的 M-203-05 以及适用于转向架的 UIC 615 等国际标准。这些标准有助于确定用于确定新部件疲劳寿命和耐久性能的测试,对于确保客运、货运和轻轨的安全、长期运营至关重要。
转向架、支撑架和侧框架认证测试要求制造商对特定配置的转向架结构和部件进行安全和可靠性测试。应用静态和动态载荷以评估性能、强度和耐久性。测试结果包括屈服和极限失效载荷水平以及疲劳寿命数据。
如需正确测试支撑架需要以下三种载荷:岩石载荷、中心反弹和边缘反弹(参见图 1)。这些载荷表示支撑架在其实际使用环境中承受的载荷。如需正确测试侧框架同样也需要三种载荷:垂向、横向和中心扭转(参见图 2)。所有这些独立的力向量对于向样件呈现适当的载荷和应力分布非常重要,有助于确保足够的疲劳寿命。
对于支撑架和侧框架的测试,适当的额定落地式载荷框架是理想的选择,而且固定相对简单。然而,转向框架的疲劳测试则更为精密复杂。转向架认证测试由国际和地方标准规定,需要的通道数量较多,工装也更为复杂。测试的载荷配置基于转向架配置。测试所需的载荷取决于每台转向架的轴数、每辆轨道车辆的转向架数,以及转向架和轨道车辆的总重量等参数。认证测试需要多通道、高载荷加载系统,且通常需要运行数百万次循环。在测试过程中,系统会收集和分析应变和其他信号,以帮助设计人员了解服务环境的载荷动态,确定高应力区域,并相应地改进设计。工程师可以通过将应变响应与有限元分析 (FEA) 模型进行比较来验证相关型号,从而改进未来的设计。
高级疲劳测试
认证标准十分严格,涉及数百万次的加载循环,但这些标准主要专注于验证足够的疲劳寿命和安全系数所需的最小载荷套组(垂向、横向和翘曲)。这些载荷明显高于正常运行期间的预期负载。加载历史记录有意保守处理,以确保在所有可能的使用组合中实现尽可能接近零的故障率。事实证明,这种方法足以满足普通货运转向架的需要,并已在全世界范围内采用(以某种形式)。
然而,在现代客运铁路机车车辆中,转向架、悬架和车厢接口比货运要复杂得多。高速客运转向架是一种复杂的焊接件。诸如阻尼器、悬架连杆和辅助部件(压缩机、制动卡钳)等零部件都会给转向架带来额外的载荷。这些载荷通常由与认证标准所述之载荷向量和位置大不相同的载荷向量和位置组成。这些载荷的位置、大小、向量和相位对于有兴趣尽可能真实地复制实际转向架运行环境的测试工程师而言是至关重要的。
在这些情况下,复杂性很快就成了问题。虽然认证测试通常使用 10 个以下通道(在大多数情况下,6 个以下),但更高级的开发测试可能需要 20 个以上(在某些情况下 30 个以上)控制通道。将额外载荷与认证标准规定的载荷结合起来,对于工装而言将是很大的挑战。
解决这一复杂问题至关重要。在过去的 10 到 15 年间,最终用户对可靠性更高、性能更佳、舒适度更优的铁道机车车辆的需求大幅增长。为满足这些需求,制造商正着手开发认证标准刚制定时尚未开发出来的材料和制造方法。用于铁路系统中几乎所有部件的设计和制造的新材料,特别是新减重方法,产生了对新开发测试程序的需求,而这些程序超出了传统认证测试的范围。
对于这些较大的结构应用,需要带有定制作动缸配置的双立柱或四立柱门式框架(参见图 3)。由于转向架上的许多载荷都很高,因此用于复制这些载荷的作动缸都很大。直接将作动缸施加到载荷点上,可能需要在同一物理空间使用多个作动缸。这一问题需要丰富的固定工装和运动机理专业知识才能解决。作动缸、杠杆、支柱(承载柱)和轴承的组合用于在正确的位置施加载荷向量。可将载荷传感器安装在作动缸、加载支柱和/或反应固定工装上。支柱和作动缸两端的旋转球铰轴承可消除侧面和弯曲载荷。在某些情况下,可能会将样件倒置,以便样件更好地进入载荷点。
交叉耦合(当一个作动缸的动作影响到另一个作动缸时)会出现严重的控制问题,必须加以克服。数字控制器和软件必须协同工作,协调受影响通道的振幅和相位,以消除干扰风险并确保准确的载荷。通常情况下,会需要先进的控制技术。整个系统,包括样件、框架和作动缸子系统,均可能具有一定的固有非线性度。考虑到这些非线性度,可能需要修改驱动信号,以便在样件上实现所需的加载历史记录。
通常使用先进的信号处理软件(如 MTS 远程参数控制 (RPC®) 软件)进行调整,该软件基于整个系统的频响函数 (FRF) 矩阵。软件会测量控制器命令,并将其与所需频率范围内样件响应的振幅和相位进行比较。生成交叉耦合矩阵,其中包括命令和响应之间的所有交叉耦合和其他线性差异。然后将该 FRF 反转并加载期望响应文件。结果会生成用于补偿交叉耦合和相关问题的作动缸驱动文件。通过计算误差,创建相应的修正文件,然后将修正应用到之前的驱动文件中,对非线性贡献进行修正。重复此迭代进程,直至实现期望精确性。应用这一控制补偿技术,可实现在更高的频率下准确运行测试,从而缩短测试时间并提高测试质量。
在这一过程中,工程师必须能够收集和管理大量数据。例如,测试系统可能需要容纳多达 250 个应变片和位移通道,以便发现设计中潜在的漏洞。其中一些数据需要实时收集以便在控制系统中使用,同时还需要收集更多数据,以便进行离线分析并与计算机辅助工程 (CAE) 模型进行比较。
克服所有这些挑战并非易事,但值得一试。零部件制造商能够利用这些结果优化设计,使新产品与众不同,并给客户带来对新零部件质量和可靠性的信心。
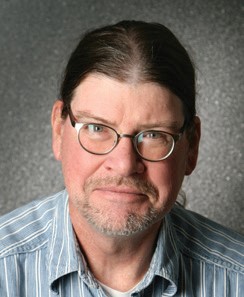