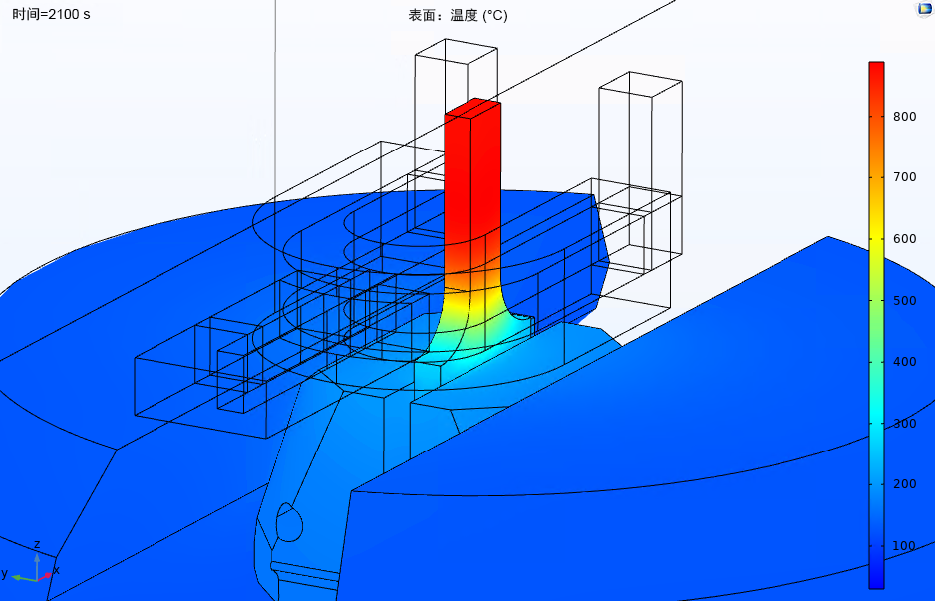
不断发展的增材制造材料标准在引发相关行业对高温下小型试样测试日益增长的需求。了解 MTS 和 TRUMPF 如何在为增材制造材料的 TMF 测试构建物理原型之前,使用多物理场仿真来预测夹具和加热线圈设计的性能。
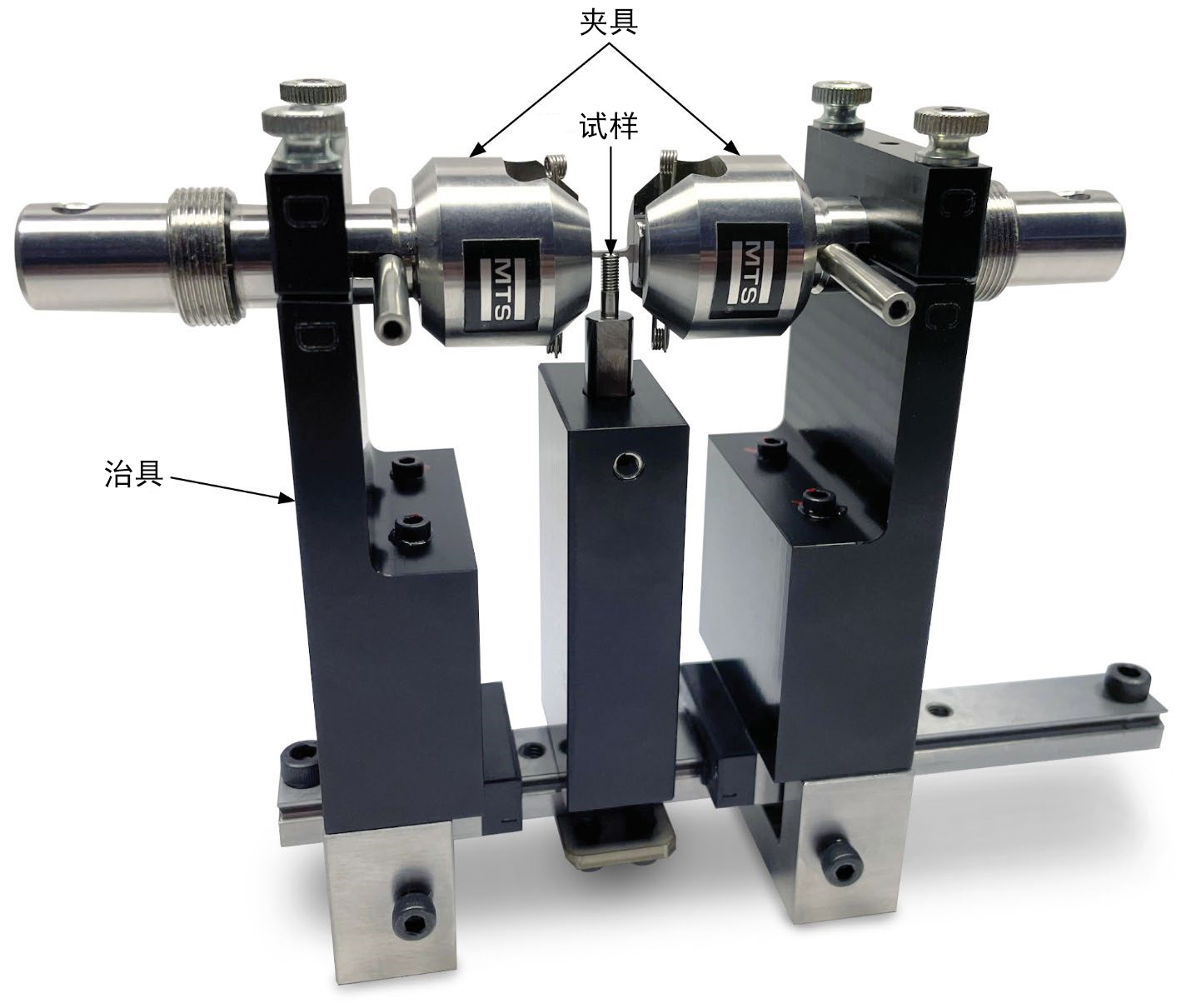
TMF 仿真概述
MTS 已经开发出面向小型试样测试的专利夹具,其静态载荷能力为 2.2 kN,动态载荷能力为 1.1 kN,分别适用于拉伸和拉-压疲劳应用。尽管如此,此类应用仍需要更大的载荷能力。对于该仿真,提出的解决方案包括一个在拉-压疲劳载荷下额定值为 5 kN 的机械夹具和一个敞开叉形感应线圈。
仿真要求
多物理场仿真的特点包括:
- 能够根据试样和线圈的几何形状做 2D 和 3D 仿真
- 通常将感应线圈的电磁场模拟为频域问题
- 可以将试样内部的温度场模拟为静态或瞬态
- 可以通过与温度相关的材料性能(例如导电性、相对导磁率、导热性、比热容)将温度场与磁场进行耦合
- 考虑通过辐射、对流和传导进行热传递
- 考虑由于使用潜在的水冷夹具而对试样产生的端部效应
加热应用的其他具体要求为:
- 最高可达到温度:900 °C
- 加热和冷却的斜坡速率:30 K/s
- 标距长度上的均匀温度分布:10 K 以内
仿真结果
借助这项仿真,MTS 和 TRUMPF 实现了以下结果:
- 温度高达 900℃
- 加热速率高达 30 K/s
- 冷却速率很大程度上取决于夹具处的温度值
- 整个标距长度上的 ΔT = 14.8 K,可以通过更新线圈设计实现更高的温度均匀型
前部敞开的叉形线圈满足了大多数加热要求以及所有可达性要求
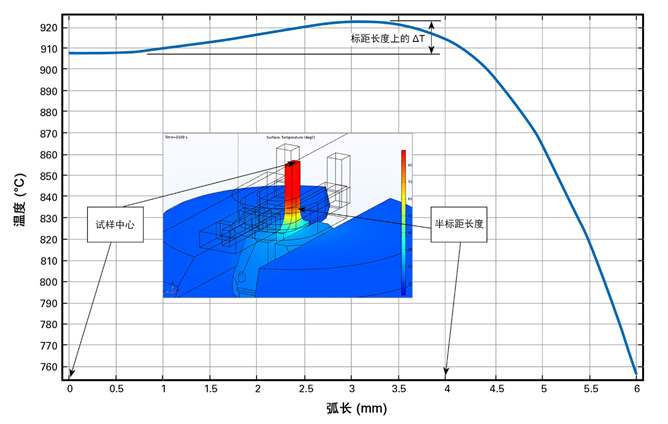
结论
仿真是一种兼顾高效率和低成本的方法,可在构建物理原型之前评估建议的夹具和加热线圈设计。MTS 和 TRUMPF 可以使用基于模型的设计来识别风险领域,并改进用于增材制造材料 TMF 测试的组件设计。