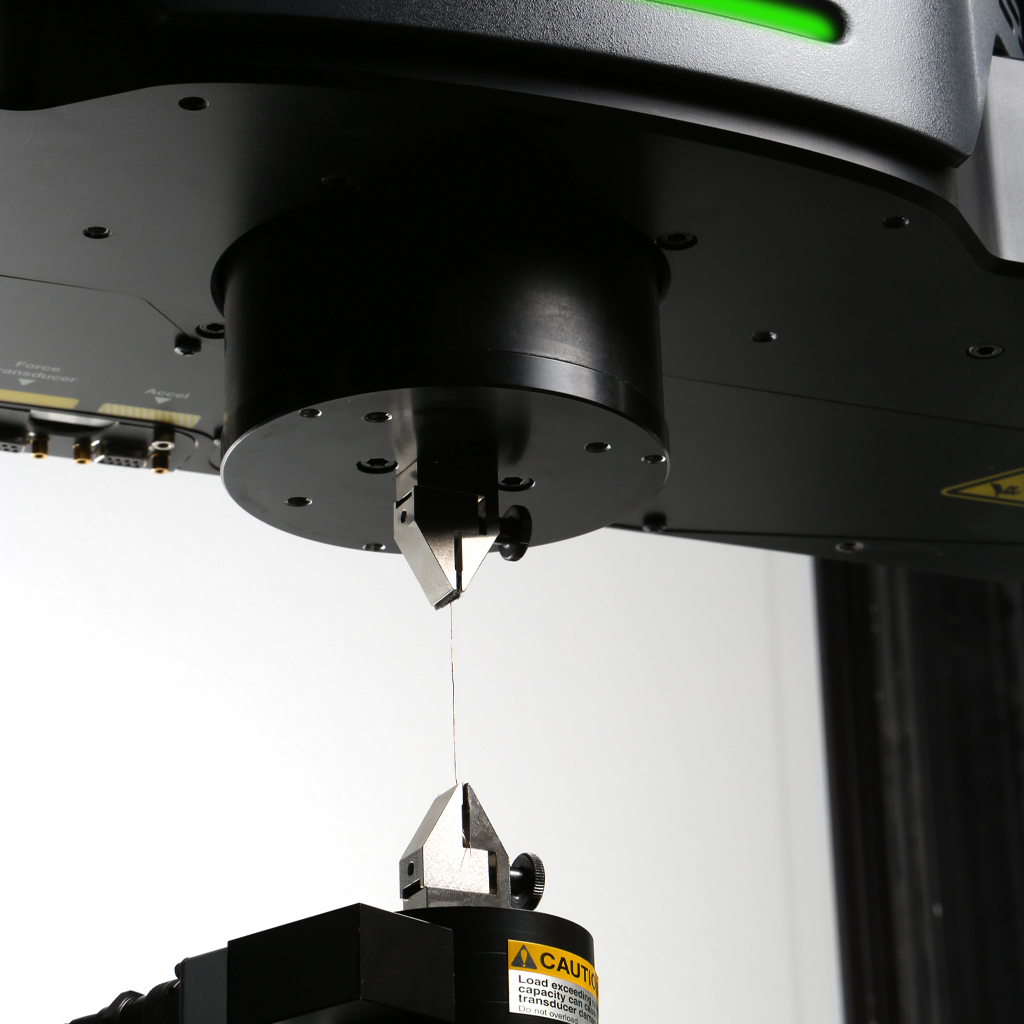
在本问答中,MTS应用工程师讨论了高强度材料和组件测试的挑战和细微差别。
问:什么是高强度测试?什么样的试件需要高力试验?
答:一般来说,任何需要超过1兆牛顿(MN)或220基普的测试都被称为高力测试。在许多行业中,高强度机械测试对于确定材料、组件和子组件的性能和耐久性至关重要,包括混凝土和钢材等建筑材料;土建结构,如梁、柱和钢筋;以及用于航空航天、石油和天然气、铁路和风力涡轮机的大型部件。本质上,如果你做一个足够大的样本,它将需要一个高强度的测试。
问:在高强度测试中最常见的应用是什么?
答:高强度应用可以从静态强度表征到复杂的动态寿命研究。由于体积效应,许多产品开发人员和制造商更喜欢测试全尺寸组件——随着材料样品或试样变大,其行为可能会发生变化。这种可变性对于某些材料尤其如此,例如铝或聚合物复合材料。
问:工程师如何使用高强度测试的数据?
答:高强度测试为开发符合预期性能的可靠结构、部件和产品提供了必要的数据。高强度测试调查并确定材料的最大应力,由于前面的答案中提到的体积效应,这可能很难预测。试样的尺寸对材料的疲劳曲线有很大的影响,这在产品设计中得到了应用。
工程师们使用高强度测试来确定材料的破坏机制是否会随着试样尺寸的不同而变化,然后创建适应这些差异的模型。对于某些材料,如聚合物复合材料,高强度动态测试可以帮助工程师了解增强纤维的编织和角度如何影响材料的最终强度和寿命。
问:MTS提供高强度解决方案有多久了?他们被部署在哪里?
答:50多年来,MTS一直致力于解决高强度测试挑战。我们是第一个将液压系统用于循环材料测试的公司,也是第一个将液压系统用于高强度测试的公司。对于客户来说,这意味着我们的团队理解所有决策的含义,这些决策必须做出,才能获得交付所需数据的解决方案。我们已经了解了哪些是有效的,哪些是无效的,并且可以帮助您在问题开始之前避免问题。
MTS已经在全球范围内部署了这些系统,用于从基础研究到识别特定材料特性的应用,今天我们在大学,政府研究中心和商业制造设施中拥有系统,包括航空航天,汽车,能源和土木工程等广泛的行业。
问:MTS为高强度测试应用提供什么样的系统?
答:MTS提供完整的标准高强度测试系统组合,可测试高达5 MN (1100 kip)的测试,并可为更高的力容量要求提供定制设计的解决方案。在这些情况下,MTS与客户密切合作,设计和建造他们的系统,例如用于进行结构钢梁弯曲测试的10 MN (2200 kip)系统,或用于进行钢筋混凝土柱压缩测试的30 MN (6600 kip)系统。测试系统可以采用传统的垂直或水平方向。
问:水平方向和垂直方向的优点是什么?
答:这取决于被测试的标本。例如,测试长电缆或石油管道的客户可能更容易使用桥式起重机将样品装载到水平框架中。相反,在垂直框架中使用压板进行压缩测试要容易得多,因为用户可以在底部压板上正确地设置和对齐样品-这在水平框架中几乎是不可能做到的。
水平高力负载框架
问:高强度测试需要特殊夹具吗?
达:是的。我们的握把的尺寸和设计可以减少高强度动态测试的质量。它们设计得很轻,以提高性能,并为客户提供尽可能宽的频率范围和最大的力。轻握可以避免浪费大量的能量来达到同样的效果。
减少质量高力握把提供广泛的频率和最大的力量
问:你们如何测量施加在试件上的力?
答:在这些高负载下准确测量力是一项独特的挑战,我们有几个不同的解决方案。MTS可以为高达30 MN的高强度测试要求制造定制的测力传感器。这些高容量力传感器可以采用多柱设计或管设计,可以抵抗外来的力和力矩,以获得更高的精度和高横向刚度。我们还有一个成本更低的解决方案,使用压力传感器根据执行器的活塞面积计算施加的力。这种“Delta P”传感器易于安装和校准,并且在高力下具有与称重传感器相似的精度。
MTS 30mn (6500 kip)称重传感器
问:你如何在高强度测试解决方案中保持正确的对准?
答:校准是至关重要的,因为试样的任何弯曲都会影响数据质量。我们的负载框架具有优越的系统对准,最大限度地减少弯曲应变,提高测试精度,减少数据分散。此外,我们还为我们的标准解决方案(高达1 MN)提供校准夹具,可以轻松检测完整仪器样品的负载序列的任何部分是否不对准。
问:与市场上的其他高力解决方案相比,MTS高力负载框架如何?
答:几十年来,为了满足现实世界的需求,许多设计改进使MTS高强度系统成为自己的一类。例如,焊接十字头具有包含系统执行器的“浴缸”设计,最大限度地减少了轴承与测试底座之间的距离,以提供更准确的结果。液压服务歧管(hsm)直接安装在框架上,并根据需要使用局部紧密耦合积累。该系统的光滑柱与夹具集成到十字头允许快速调整十字头高度。所有这些设计元素体现在系统的无与伦比的实用性和坚固性,以及其运行疲劳测试的能力,以框架的全力额定值很长一段时间。
问:高载荷框架系统是否存在独特的设施挑战?
答:是的,这很有挑战性。我们不得不拆除建筑物的屋顶,用起重机把系统搬进去。安装这些高强度测试解决方案通常需要广泛的系统集成专业知识。例如,我们向台湾的一家工厂交付了一个30 MN的系统,在那里我们集成了明尼阿波利斯设计的组件,并由全球各地的供应商制造。即使对于较小的高强度系统,设施设计也起着重要作用。系统的底板往往必须与建筑物的楼板融为一体。我们有丰富的经验来指导客户完成整个过程,因此他们了解如何为成功的安装和测试操作准备设施。
立即联系MTS,了解如何从MTS数十年的高强度测试专业知识中获益。