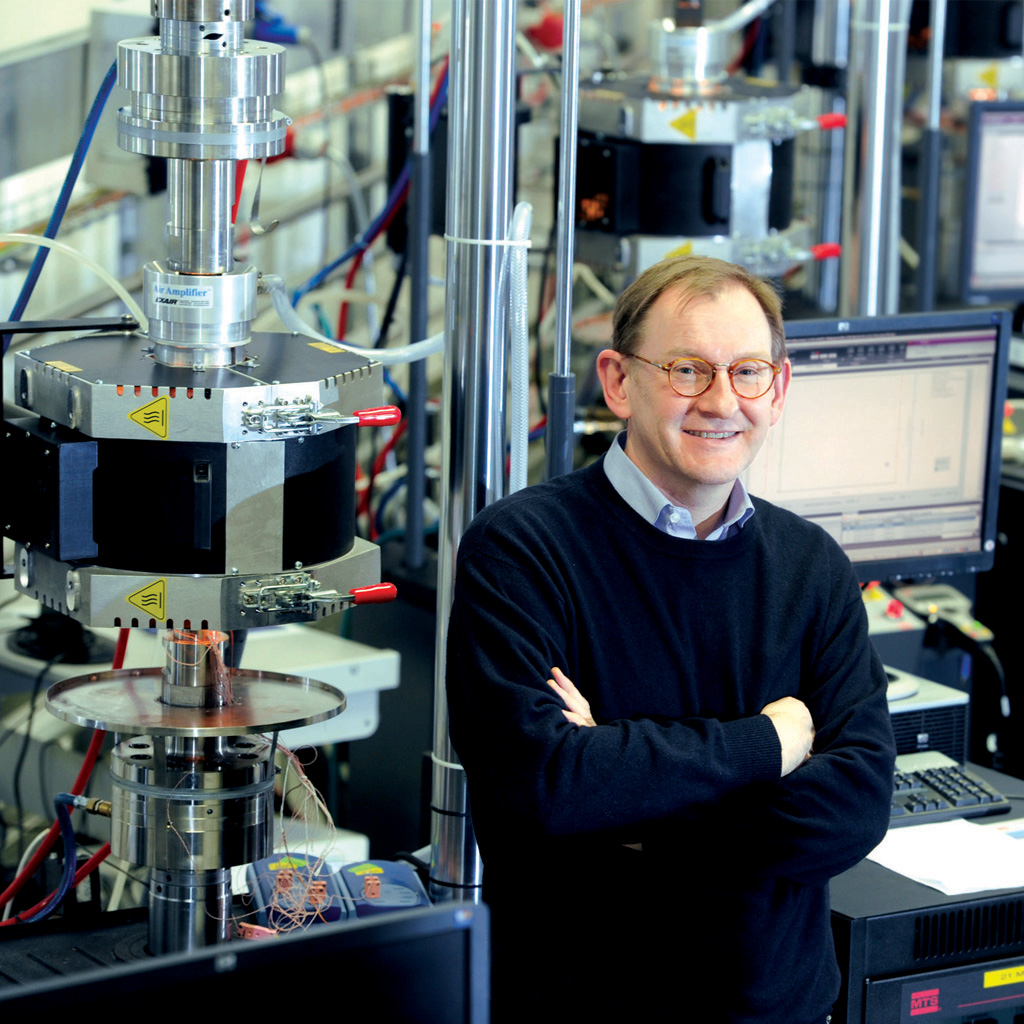
客户面临的挑战
罗尔斯·罗伊斯的先进力学测试中心(MTOC)是由罗尔斯·罗伊斯公司投资兴建的一家致力于航空发动机技术创新的研发机构。他们关注先进涡轮风扇航空发动机材料与结构等方面的研究,通过大量的材料力学与结构振动测试来指导航空发动机的研发、生产与服役过程。罗尔斯·罗伊斯投资兴建该试验室有两个目标:满足产品创新和后市场服务的迫切需求, 同时将所有材料力学和振动测试都集中在同一家试验中心。
先进力学测试中心于 2010 年正式投入使用,可开展一系列针对航空发动机的测试,例如风扇叶片脱落、鸟撞或吸入飞鸟、高速旋转、疲劳耐久、振动,当然还有基础材料力学测试。测试中心占地接近7,000m2,有 70 余名员工,位于柏林附近的达勒维茨,邻近罗尔斯·罗伊斯公司的业务合作伙伴和供应商。
热机械耦合疲劳 (TMF) 试验是先进力学测试中心开展的最重要的测试项目之一。热机械耦合疲劳能够准确复现涡轮发动机内部的工作环境。利用该测试产出的结果,罗尔斯·罗伊斯公司研发人员就能够尽早深入了解新材料的特性,评估全新材料在服役条件下的表现,就能够严格控制工艺流程,提升产品质量,让航空发动机寿命更长,可靠性更高。但是,热机械耦合疲劳测试却又是复杂的试验项目,充满了不确定性和挑战。
“我们所要求的测试项目非常复杂,需要将温度循环和载荷循环保持严格的相位关系,这并不是简单感应加热式高温测试,” MTOC 测试工程师和 TMF 测试专家Stephen Brookes 博士说道,“MTOC 开展的 TMF 测试包括应变控制和应力控制两种模式,这两种模式的控制过程不同,但是都很复杂而且有难度。而我的职责就是确保这些复杂的测试任务能够准确、可靠并且高效的完成,还能够不断发展。”
MTS 解决方案
为了能够实现复杂的热机械耦合疲劳测试任务,先进力学测试中心决定与MTS合作,使用MTS所提供的力学测试解决方案。如 Brookes 博士所说,他们开发的热机械耦合疲劳测试具有两种模式,一种是应变控制热机械耦合疲劳,而另一种是应力控制热机械耦合疲劳。他们选择使用了MTS Landmark®电液伺服力学测试系统作为基础配合定制的附件来实现这些相关的测试任务。
MTS Landmark 电液伺服力学测试具有集成化的控制能力,完整的解决方案包括370型电液伺服加载框架、MTS FlexTest®数字控制器以及应用软件,MTS SilentFlo ™液压动力源提供持续的动力支持。定制的感应加热子系统和冷却系统实现可控的温度循环,MTS系统公司为力学测试中心的热机械耦合疲劳测试量身定制了夹具和引伸计。
MTS TestSuite ™试验应用软件提供了热机械耦合疲劳测试模块,该模块包含了进行热机械耦合疲劳测试所需要的执行试验、分析数据和自动报告生成全部功能。通过预先定制的测试应用模板,可以直接用于运行符合ASTM或者ISO标准的试验应用,也可以通过简要的修改来满足定制化的需要 ,这些测试不仅仅是单轴测试,也可以实现多轴的材料力学测试。
客户的收益
“MTS 系统公司的产品设计非常棒,” Brookes 博士夸赞道,“全面考虑了实现精确测试的方方面面,加载框架、高温炉和冷却系统全部通过TestSuite 软件集成和控制。这让我们能够准确、高效地进行测试,重复性和可靠性非常好。”
根据 Brookes 博士的观点,MTSTestSuite 应用软件非常通用而且多样化。
“如果我们的需求发生了变化,我们可以很容易通过创建新的测试流程或者改写现有的测试流程来实现它,而不需要我们考虑很多关于加载框架、高温炉和冷却系统的细节,这对我们很重要。这让我们很快就完成了应力控制的热机械耦合疲劳测试,我们认为难以实现的同步控制问题对于MTS的系统来说好像不是什么难题。”
MTS 系统公司的人员具有丰富的专业知识他们帮助先进力学测试中心实现了特定的目标。
“我们很高兴能够有 MTS的软件开发人员为我们开发应变控制的 TMF 模板程序,” Brookes 博士说,“事实证明这种开发方式非常有效,尽管我们试验中心距离 MTS 空间上很远,但是,从我们提出要求到得到 MTS 的反馈,却非常快。”
Brookes 博士对热机械耦合疲劳测试的未来发展以及MTS 测试系统在先进力学测试中心中所能够发挥的作用持乐观态度。
“在 MTOC,TMF 测试的发展将延伸至更复杂的应用,引领更进一步的技术发展,” Brookes 表示,“将不同的测试类型整合到 TMF 测试,例如疲劳裂纹扩展与TMF相结合,这就是增加测试复杂度的一个例子。从试验技术开发的角度来看,改进实践、创新测试监控技术和开发新标准方面始终具备空间。我们现在有了MTS,我认为这些未来的愿景没有理由不成为现实。”